Affordable Continuous Automated Vibration Machine Monitoring to
Zero In On Machine Problems
Use Analyst Inside as your early warning tool to find that one machine out of hundreds that actually has a problem.
Schedule a DemoDon’t Put Your Reputation at Risk Because You Didn’t Catch an Issue
As a Vibration Analyst it’s difficult to keep up with all the data putting you at risk of missing something…
Your customers will start looking at alternatives
You’re burned out sifting through all the data
You’ll have upset customers that you could lose
You'll feel guilty for not using every technique
You’re wasting time on machines without problems
You're worried that you don’t have current data
You don’t have to constantly be on site to do your job. Using the power of Analyst Inside you get around the clock monitoring to point you to the machines that have problems - so you can provide better and more timely recommendations.
Expand Your Business and Improve Your Profitability with Analyst Inside
Schedule a Demo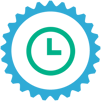
Eliminate Wasted Time
Free up time spent analyzing good machines to focus on the machines that have problems.
Serve More Customers
Improve your service and be confident in your ability to retain and expand your customer base.
Be Recognized As The
Expert You Are
Provide more timely advice and recommendations that will reinforce your value to your customers.
How it Works

Gather Vibration Data
Get real-time vibration data from your machines.

Continuously Analyze Data
Analyze the data 24/7 using standard vibration analysis techniques.

Get Actionable Alerts
Receive notifications when a machine issue is detected & recommendations to address the issue.
We understand how challenging it can be to try to keep up with all the data all the time. We can help.

Data collected and analysis performed in real-time

System developed by level 3 Certified Vibration Analysts

Patented Technology Uses 20+ Proven Vibration Analysis Techniques
Automated Vibration Machine
Monitoring Options
Montoring OptionsBasic Monitoring
Monitor two points with single axis accelerometers, mounted on the motor and load OR both on the motor. Sufficient to monitor and detect issues before they result in unplanned downtime.
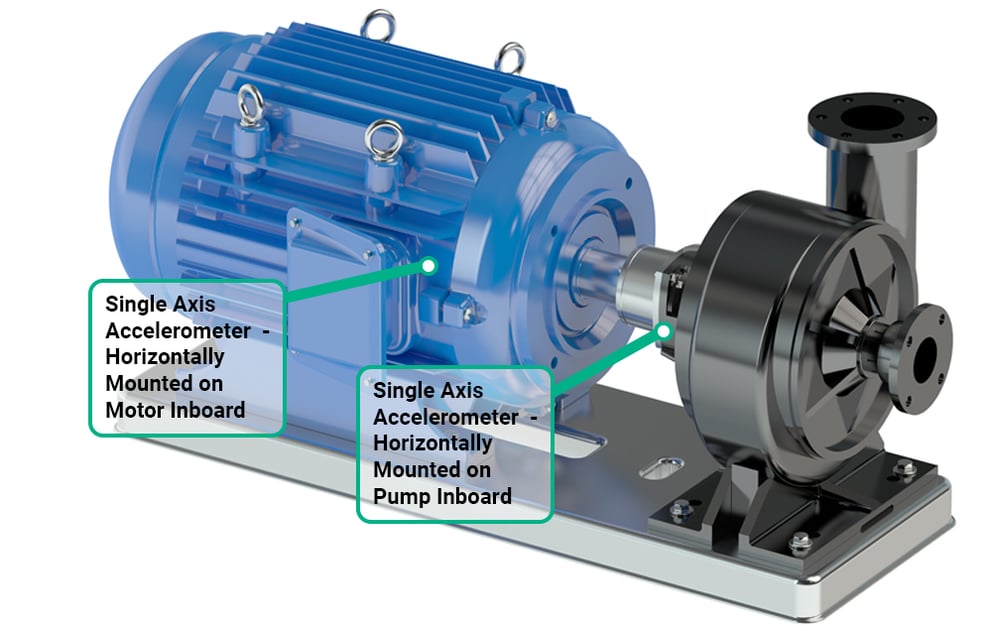
Montoring OptionsAdvanced Monitoring
Monitor four to six points, minimum of two on the motor and two on the load to provide additional coverage of machines that have a higher cost of failure if they go down. With the additional monitoring points, you will be able to detect issues sooner.

Montoring OptionsCritical Monitoring
By using triaxial accelerometers (which measure three points of vibration --- one each in the x-y-z axis), measure six points on the motor, and six points on the load to provide complete coverage of your most critical assets. With the additional monitoring points you will be able to detect issues sooner and have more detailed information on what needs attention.
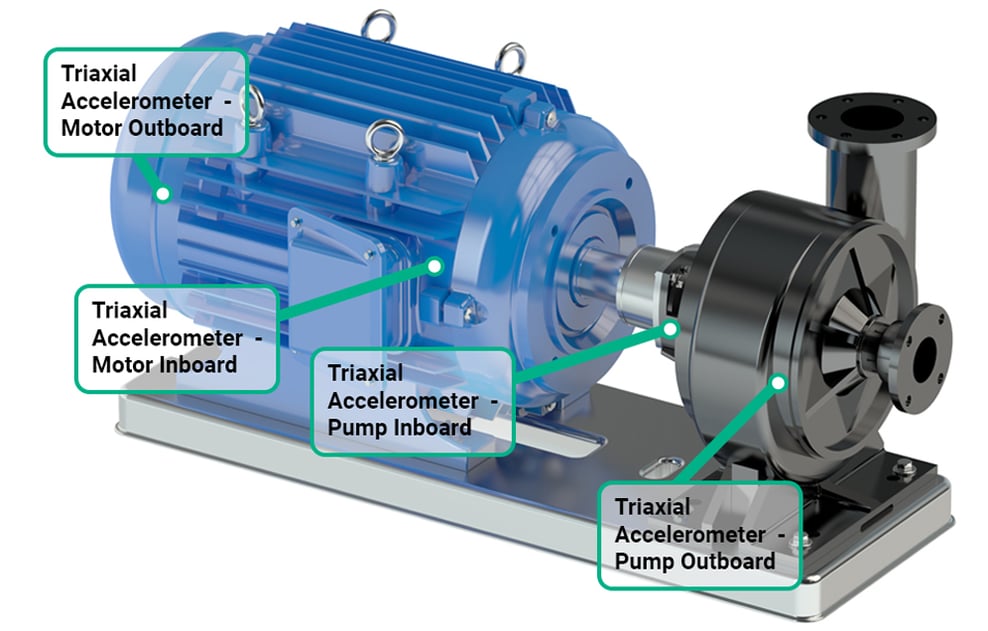
Stop Analyzing Machines That Are Working Well And Focus On The Machines That Need Attention
You’re responsible for hundreds of assets and it takes hours to do a thorough analysis on a single machine. Most of the time the analysis won’t reveal anything because the machine is fine, meaning you just lost valuable time. With Analyst Inside, you’ll be directed to the machines that have the issues as soon as they occur. It’s your around the clock watchdog that enables to you to do a better job.
Because of the sheer volume of data you’ve gathered and the time it would take to run a dozen or more analysis techniques, you’re forced to settle for just taking a quick look at some of the key pieces of data. If nothing looks “significant” you’ll move on. If something does look odd, that’s when you’ll dig in to look at additional data and perform additional analysis.
But what if that quick look resulted in overlooking some key information that would have pointed to an emerging machine issue? Best case, nothing bad happens before you get a chance to get back to the plant next month to take more readings that might alert you to an issue. Worst case though, you miss the issue and don’t notify your customer. The machine breaks down and they begin to wonder why they are paying you.
Perhaps you are able to perform the thorough analysis that you want. But what happens if the problem started the moment you left the plant after running your route? Now it’s not a question of having the time to do a thorough analysis…you’ve just done a thorough analysis on stale data. The result is the same…you aren’t able to give your customer the “heads up” on the problem.
Nothing is more frustrating than having your credibility undermined by missing a problem that you could have detected if you would have had more time or more recent data.
With Analyst Inside, you’ll have an onsite analyst doing all of the analysis that you wish you had the time to do with the most recent data. When it detects anything, it will let you know. Then you’ll know exactly where to look if further investigation is needed. Think about it - you’ll be able to improve your diagnosis and recommended corrective actions as soon as problems arrive, instead of waiting for the monthly report to be finalized.
So what will you do with all of the time that’s been freed up because you’re not analyzing machines that don’t have any problems? Perhaps for the first time in a long while you’ll be able to take on additional customers and grow your business, all the while providing superior service above you could have previously.
Consider Analyst Inside another powerful tool in your toolbox.
Stop feeling overwhelmed and frustrated with all of the time it takes to gather and analyze the data. Become the hero for your customer that detects problems as soon as they begin and offers solutions to correct them.
In many cases, Analyst Inside will begin detecting latent machine issues sooner than a monthly vibration service ever would.
And if you are worried that this is some cloud-based solution where your data will be beamed out of the plant, fear not! Analyst Inside resides in the plant and all data stays on the module. It’s your data, you decide how to use it and where to send it. Unlike other solutions, there is no monthly monitoring fee to worry about (and the real possibility of losing access to historical data if you decide to stop paying for the service). You buy the equipment once. It’s yours, and so is your data.
You deserve to have a drama-free, no-surprises operation, so schedule a 30 minute demo to learn more.
Schedule a DemoRead More