Affordable Continuous Automated Vibration Machine Monitoring to
Eliminate Costly Unplanned Downtime
And Meet Your Plant's Monthly Goals
Schedule a DemoDon’t Let Unexpected Machine Failures
Catch You Off Guard
Reacting to machine failures will put your plant operations in a state of chaos…
You’ll pay extra for emergency repairs
You’re breaking delivery promises
You're constantly putting out fires
You might be endangering your employees
You’re losing valuable production time
You’ll experience quality problems that create waste
Leaving machine failures to happen by chance is like a ticking time bomb waiting to explode. With Analyst Inside you get more accurate around the clock monitoring with actionable recommendations on how to correct machines problems that are detected – and you’ll actually know what’s wrong to defuse problems before they happen.
Achieve Drama-Free, No-Suprise Operation with Analyst Inside
Schedule a DemoAvoid Disasters
Stop reacting to disasters and prevent them instead with advanced warnings when machines have issues.
Save Money on Machine Maintenance
Address small problems before they become costly.
Operate with Confidence
Eliminate unplanned downtime and keep your plant running smoothly.
How it Works

Gather Vibration Data
Get real-time vibration data from your machines.

Continuously Analyze Data
Analyze the data 24/7 using standard vibration analysis techniques.

Get Actionable Alerts
Receive notifications when a machine issue is detected & recommendations to address the issue.
No one likes plant operations interrupted by unexpected machine failures

Saved over $18 Million in Unplanned Downtime

Over 30 Years of Experience in Industrial Automation

Patented Technology Uses 20+ Proven Vibration Analysis Techniques
Automated Vibration Machine
Monitoring Options
Montoring OptionsBasic Monitoring
Monitor two points with single axis accelerometers, mounted on the motor and load OR both on the motor. Sufficient to monitor and detect issues before they result in unplanned downtime.
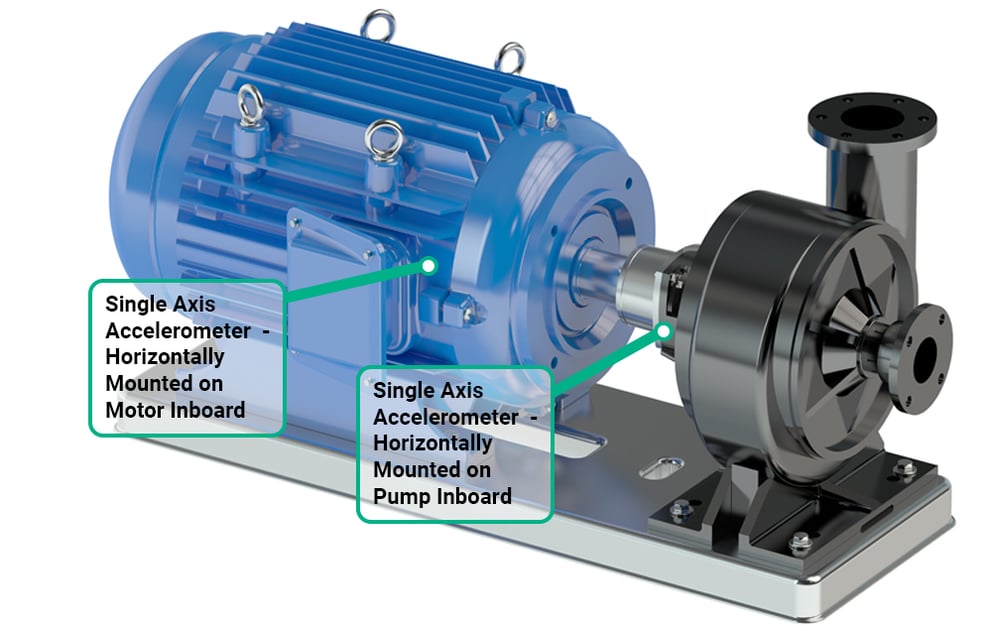
Montoring OptionsAdvanced Monitoring
Monitor four to six points, minimum of two on the motor and two on the load to provide additional coverage of machines that have a higher cost of failure if they go down. With the additional monitoring points, you will be able to detect issues sooner.

Montoring OptionsCritical Monitoring
By using triaxial accelerometers (which measure three points of vibration --- one each in the x-y-z axis), measure six points on the motor, and six points on the load to provide complete coverage of your most critical assets. With the additional monitoring points you will be able to detect issues sooner and have more detailed information on what needs attention.
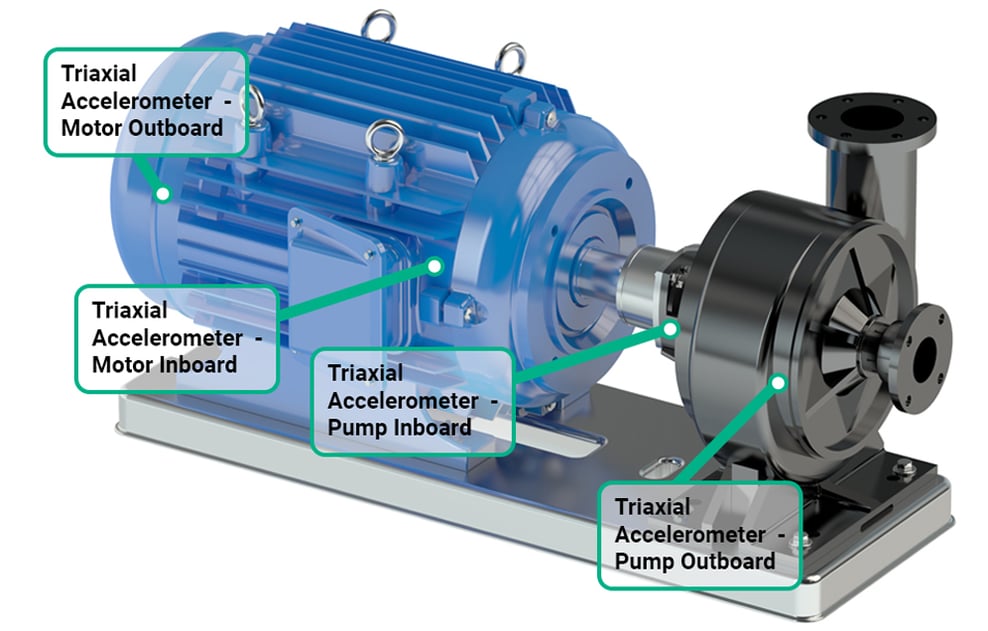
Stop being a victim of machine issues and take control with Analyst Inside
You’ve got your production schedules all set. Your shifts are staffed and you’ve got the raw material ready to go. You’ve committed delivery dates to all of your customers. What could go wrong? A machine issue has been quietly developing undetected. And if you don’t know about it, you can’t fix it. You can all but guarantee the machine will fail at exactly the wrong time, throwing all of your plans into chaos. By deploying Analyst Inside, you can detect issues that are developing BEFORE they lead to costly unplanned downtime. The result is a plant that runs as you planned with no surprises.
There’s a lot that goes into a safe, well-run, profitable plant. Most of the time, the attention is on all of the things that you need to do to make the plant run, NOT on the things that could bring the plant to its knees. You hope that the preventative maintenance programs will be sufficient to keep all of your equipment in good working order. Until it doesn’t.
Problems can develop in between maintenance cycles. But you know that, so maybe you have already invested in some form of machine monitoring. The most common is using a vibration monitoring service that gathers data once a month and provides an analysis a few weeks later. This still leaves you vulnerable to a machine developing a problem that will get missed. Analyst Inside continuously gathers and analyzes vibration data. As soon as it detects something that needs your attention, it sends your maintenance team an email or text notification. No more surprises that a machine is having an issue and might go down when you least need it to.
Other continuous monitoring high-end systems can be expensive, difficult to set-up, and still need a trained vibration specialist to interpret results. With Analyst Inside you’ll get a system that is cost effective, easy to set-up, and specific actionable recommendations without needing to be a trained vibration analyst to understand. Your maintenance team will love the “plain English” recommendations on what they need to do.
Unlike other solutions, there is no monthly monitoring fee to worry about (and the real possibility of losing access to historical data if you decide to stop using the service). You buy the equipment once. It’s yours, and so is your data. On average, Analyst Inside customers can expect a payback on their investment in less than a year (and in many cases, just a few months)
You deserve to have your plant run as planned. So schedule a 30 minute demo to learn more.
Schedule a DemoRead More